Best Practices in Supply Chain Planning
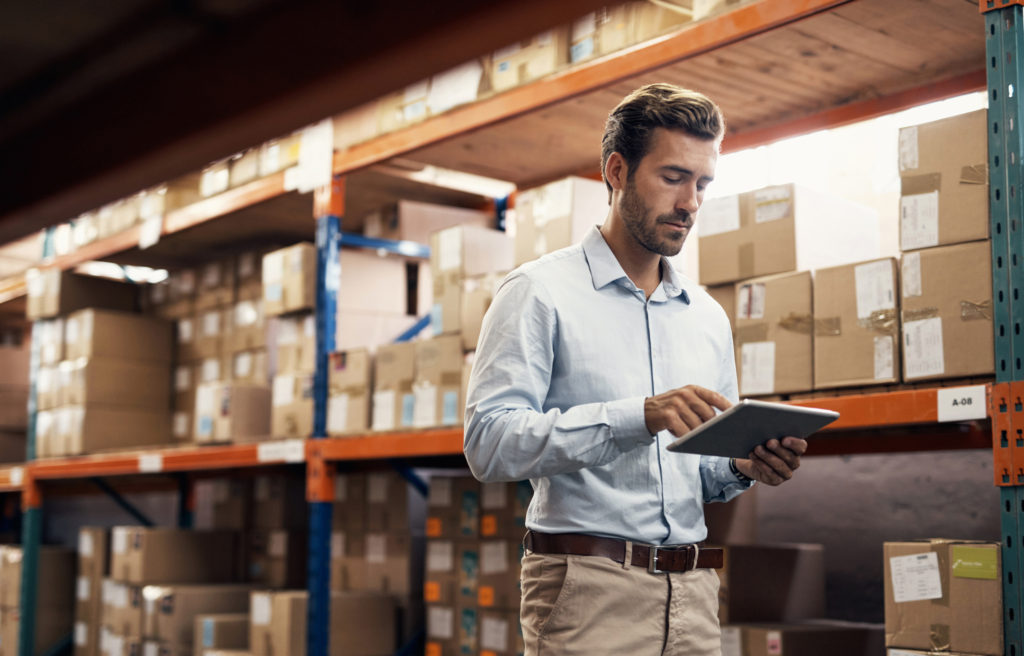

Generating a trusted forecast for demand and supply even while incorporating uncertainty and optimizing inventory can seem like a daunting task…or is it? For many supply chain planners, it looks that way at first glance because forecasting and managing sales/demand planning, supply, production and sales and operations planning (S&OP) is rife with uncertainty and risk.
Adopting a best-practice approach to supply chain planning and using the right tools will make your job easier by automating forecast, uncertainty estimation and risk-adjusted decision optimization. Here are four steps to keep in mind for supply chain planning:
The first step in supply chain planning is to understand the types of uncertainties your organization faces. Uncertainties are events that are ambiguous or unpredictable. For example, is it that we don’t know what next month’s demand will be, or that we don’t know exactly when to expect an order from a vendor? Then think about how you currently incorporate these uncertainties into your planning process. For example, how do you take demand uncertainty and use it in your planning models or your planning process?
The second step is to ask similar questions about risks. Risk is the exposure to loss or factors and events that could result in not achieving goals and ultimately how the business is impacted. The risk is more about the business outcome. If demand comes in higher than I expected and I don’t have enough inventory, then I risk losing revenue because customers can’t buy the product I want them to buy. So how do you incorporate these risks into your planning process? Will demand be higher than expected? What if I don’t have enough inventory? Then I risk losing revenue.
The third step is considering how you are incorporating these uncertainties and risks into your planning process. This can be a challenge for a lot of organizations, especially if you are not used to doing it. Are you truly modeling and planning to incorporate uncertainties, or are you making best guesses and assumptions?
The fourth step is finding the appropriate forecasting method for your organization. There are many different forecast models, but they generally boil down to four main categories with pros and cons for each:
- Point Estimate – very easy to understand, but there is no sense of range, variance or likelihood
- Range – easy to understand, hard to implement
- Best, Worst and Most Likely – commonly used in planning, analysis is often incorrect and can be misleading
- Probability Distribution – conceptually its easy, real probability distributions are complicated and hard to implement
Each model clearly has its pros and cons, but here are two quick and important tips on the methods as we traverse the list from top to bottom:
- It becomes apparent that using only an average for forecasting is flawed
- We can easily recognize our brains inherently tend to shy away from predicting uncertainties and risks without the right tools and information
In conclusion, the fundamental challenge supply chain planning professionals face today is uncertainty. And as much as we would like to eradicate uncertainty in the supply chain, we simply can’t. However, there are things we can do. Smarter supply chain planning allows planners to quickly work with suppliers to acquire scarce inbound materials. Visibility to supply requirements over a longer horizon allows for long-range planning alongside shorter-term decisions, making plans more reliable. The latest software technology can be helpful, especially in combination with the current plan, which provides visibility on future stock projection and can be combined with a supplier calendar for even more visibility.
While sometimes you know roughly what to expect, as in seasonal variability, there are many instances in which you can’t predict what might happen. Often, there is little time to prepare, so supply chain planners must make quick, effective decisions in the face of uncertainty.